How to Use Glow-in-the-Dark Pigments
October 10th, 2024Glow-in-the-dark pigments, also known as phosphorescent pigments, have many uses. From creating glow-in-the-dark plastic products to increasing decorative object visual appeal and more. Proper application of glow-in-the-dark pigments is key to producing optimal glow effects – here is a comprehensive guide on how you can use glow-in-the-dark pigments effectively.
Long-Lasting Glow Technology for Plastics
Glow-in-the-dark pigments can be utilized in various plastic processing techniques such as injection molding, extrusion, casting, calendering and mixing. A recommended practice is to first create phosphorescent plastic masterbatches – intermediate products made by mixing pigment with plastic resin – which maximize the glow effect by evenly dispersing its pigment throughout the material.
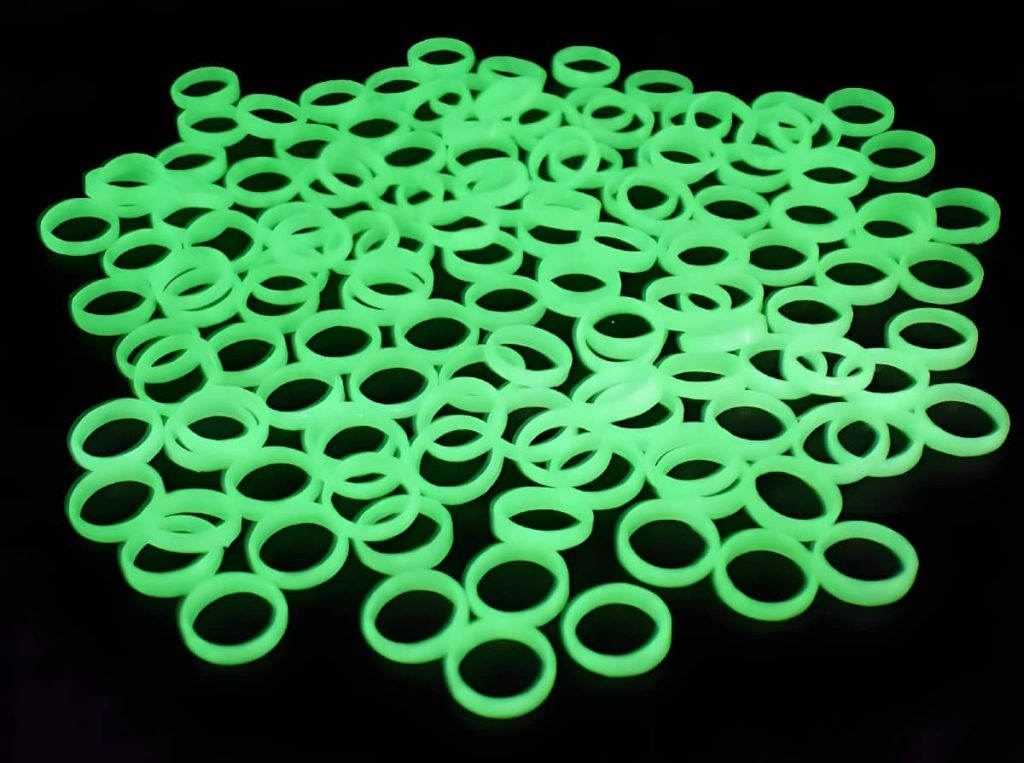
Glow Pigment Preparation Method
For optimal results when using glow pigments, follow these preparation steps.
- Utilize High-Quality Equipment: Select equipment with smooth surfaces in order to minimize friction, as too much may damage both the equipment and pigment, leading to contamination and eventually leading to its degradation. Smooth machinery also contributes to an enhanced glow effect in final result.
- Avoid Filters Containing Coarse Pigment Particles:
As glow-in-the-dark pigments have larger particles, use screw machines without filtering screens when producing masterbatches to process. Filtering screens could trap pigment particles and result in inconsistent glow patterns. - Injection Molding Process:
With injection molding, you can achieve a one-step process. Just coat plastic particles evenly with pigment before adding dispersing agents like white oil or polyethylene wax for enhanced flow and adhesion properties of the mixture. - Masterbatches to Enhance Glow:
When creating glowing plastic products, masterbatches provide superior performance. These intermediate materials can be used to produce glowing sheets, pipes, wires and more – always create masterbatches before processing the final product for best results! - Avoid Contact with Iron:
Long-lasting glow pigments should avoid coming into direct contact with iron as high-speed friction could darken them over time and diminish their glow. - Recommended Pigment-to-Plastic Ratio:
As a general guideline, when mixing glow pigment with plastic materials such as silicone or rubber, adding between 4-8% pigment ensures that the final product has an optimal combination of bright illumination and long-term strength without compromise to strength or flexibility of material.
Tips for Utilizing Glow Pigments in Production
- Avoid Rough Equipment or Complex Processes: Rough surfaces or overly complex machinery setups may impede the effectiveness of glow pigment. For best results, opt for equipment which promotes smooth processing for optimal results.
- Avoid Metal Containers for Mixing:
When mixing glow pigments, be careful to use only nonmetallic containers and mixers – metal may impede with how the pigment reacts and may result in unwanted chemical reactions that lead to discoloration or reduced luminescence. Rather, opt for nonmetallic lined containers which prevent unwanted reactions that could result in discoloration or reduced glow intensity. - Select Transparent Resins:
To create masterbatches that illuminate, choose transparent resins like polypropylene (PP), polystyrene (PS), acrylonitrile styrene (AS), or polycarbonate (PC), all with high levels of transparency – the more translucent, the greater its glow effect; however, opaque resins like ABS may also be used but their effects may be less intense. - Temperature Control: To create the ideal masterbatches or products, mix all materials evenly before processing in an extruder. Lower the processing temperature 20 degrees below what would normally be set by resin manufacturers to protect glow pigment from degradation; maintaining proper temperature regulation ensures its ability to glow for years afterward.
Steps for Material Prepation
Weight the glow pigment (approximately 2-10% of total mixture).
Add a small amount of dispersing oil (such as paraffin or white oil ) to the pigment and mix thoroughly until a paste has formed.
While stirring, gradually incorporate paste into base resin.
Add color pigments (preferably fluorescent hues) gradually, while making sure that glow pigment remains the primary component.
Avoid overmixing to prevent pigment from settling at the bottom, and check that no heavy metals such as iron come into contact with it that might darken its hues.
Recommended Plastic Materials: Glow-in-the-dark pigments work best when added to materials like PP, PE, PVC, PU, PS, ABS, TPR, EVA, PMMA and nylon plastics; transparent ones will produce brighter glow effects than opaque ones. When adding color pigments try not to exceed what would otherwise be necessary – adding too many can decrease its brightness! When adding colored pigments aim for minimal usage so as not to diminish it!
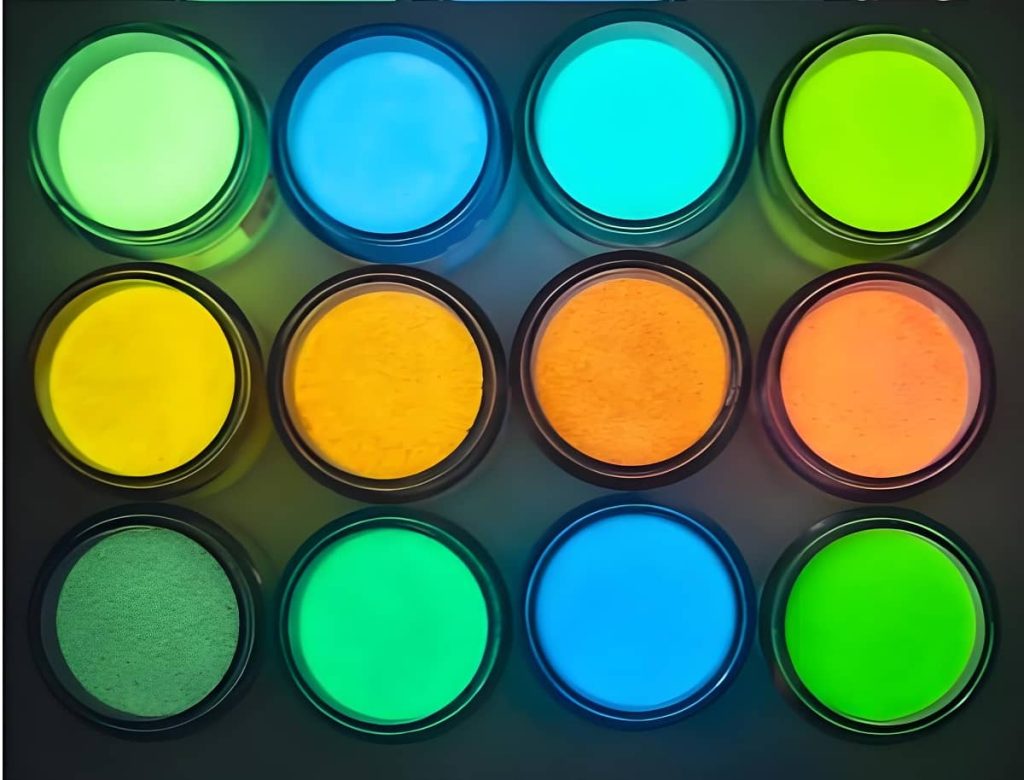
Mold Injection with Glow Pigments
- Temperature Adjustments: To optimize performance when using an injection molding machine, set it at its lowest functional temperature setting to prevent your glow pigment from overheating, leading to either charring or decreased glow intensity.
- Processing Time:
Be wary of leaving material in an injection molding machine for too long as overheating could compromise both its quality and brightness, leading to lower quality products. - Machine Differences:
Be mindful that the performance of glow-in-the-dark pigments varies based on the type and condition of injection molding machine you use for production. Newer machines, older machines, domestic models, and imported models all can produce differing results; adjustments may be needed during production to optimize their glow effect.
Glow Pigments Can Present with Issues
Due to several variables, such as machine type and production techniques, glow-in-the-dark pigments may occasionally produce unfavorable or uneven finishes. By experimenting with various settings and closely overseeing production processes, you can achieve optimal results for your unique setup.